Understanding Externally Influenced Corrosion and How to Mitigate It
Corrosion is a common issue in the offshores oil and gas environments, leading to the premature failure of essential components. According to NACE study*, the global cost of corrosion is estimated to be US$2.5 trillion, which is equivalent to 3.4% of the global GDP.
Understanding the different types of externally influenced corrosion is crucial for proper mitigation. There are four primary types of external corrosion, namely general (or uniform) corrosion, galvanic corrosion, locally influenced corrosion, and stress corrosion cracking.
1. General (or Uniform) Corrosion
General corrosion is the most well-known type of corrosion is also the easiest to spot and predict. In a marine or other corrosive environment, the surface of carbon or low-alloy steel begins to break down, allowing for the formation of an iron oxide scale which grows thicker in time until it spalls off and new scale forms. In this scenario, using a thicker component is potentially a straightforward and effective mitigation strategy. By selecting a thick component, you ensure that even as corrosion progresses, enough material remains functional throughout the lifetime of the component.
Another way to mitigate general corrosion is painting the component. That will help create a barrier against corrosive elements, thus prolonging its life. For those seeking more durable solutions, choosing a corrosion-resistant alloy can significantly reduce the rate of general corrosion, enhancing overall longevity.
>Potential Solutions: 316/316L; 6-Moly Alloys; Alloy 2507; Alloy 825; Alloy 625; Alloy C-276; Alloy 400
2. Galvanic Corrosion
Galvanic corrosion occurs when two metals with a dissimilar electrode potential are in contact in the presence of an electrolyte, such as a bolt holding two plates. If one of these materials is more susceptible to corrosion than the other, the more susceptible metal will corrode faster, leading to premature failure.
To mitigate galvanic corrosion, proper material selection is paramount. Ensure that the materials you choose are compatible and avoid coupling metals with a significant difference in their electrode potentials. Choose materials with a voltage difference that does not exceed 0.2V can also significantly reduce the risk of galvanic effects.
3. Localized Corrosion: Pitting and Crevice Corrosion
Localized corrosion encompasses pitting and crevice corrosion, both types of corrosion are more difficult to detect than general corrosion, making them more challenging to identify, predict, and design against. It occurs as the material’s protective oxide layer breaks down when it is exposed to fluids which contain chlorides. This film typically offers a level of protection but can become compromised in harsh environments. The use of higher chromium stainless steels is a key mitigation strategy, as the enhanced chromium content strengthens the passive oxide layer, thereby improving resistance to locally influenced corrosion.
Moreover, increasing the content of molybdenum and nitrogen can further enhance the robustness of the passive film, effectively reducing the likelihood of pitting and crevice corrosion.
>Potential solutions: 6-Moly Alloys; Alloy 2507; Alloy 825; Alloy 625; Alloy C-276; Alloy 400
4. Stress Corrosion Cracking (SCC)
Stress corrosion cracking (SCC) arises in components under stress and exposed to chlorides or dissolved salt in seawater. This combination can activate a corrosive attack that leads to severe cracking. SCC is dangerous because it can destroy a component at stress levels below the yield strength of an alloy.
In the presence of chloride ions, austenitic stainless steels are susceptible to SCC. The ions interact with the material at the tip of a crack where tensile stresses are highest, making it easier for the crack to grow. While in progress, SCC can be difficult to detect, and final failure can occur suddenly.
To combat stress corrosion cracking, increasing the nickel content within the material can significantly improve resistance. In fact, using nickel-based alloys can provide substantial immunity against chloride stress corrosion. Another effective option is duplex stainless steel, which combines a balanced ratio of ferrite and austenite, providing excellent resistance to chloride stress corrosion cracking while maintaining lower nickel content.
>Potential Solutions: 6-Moly Alloys; Alloy 2507; Alloy 825; Alloy 625; Alloy C-276; Alloy 400
At Swagelok Malaysia, we understand the importance of addressing corrosion challenges within various applications, especially in the offshore environment. With Swagelok's commitment to higher material specifications—such as a minimum of 17% chromium and 12% nickel—we ensure our products meet and exceed industry standards for corrosion resistance. By leveraging enhanced chemistries, we can provide solutions tailored to withstand the demanding conditions of your applications.
Investing in the right strategies for corrosion mitigation not only prolongs the life of components but also enhances safety and reliability in your plant’s operations.
Contact Swagelok Malaysia today to learn more about our corrosion-resistant products and discover how we can support your industrial operations against corrosion challenges.
Related Articles

Pitting Corrosion vs. Crevice Corrosion
Corrosion—the deterioration of engineered materials by chemical interaction with their environment—is an extraordinarily costly problem.
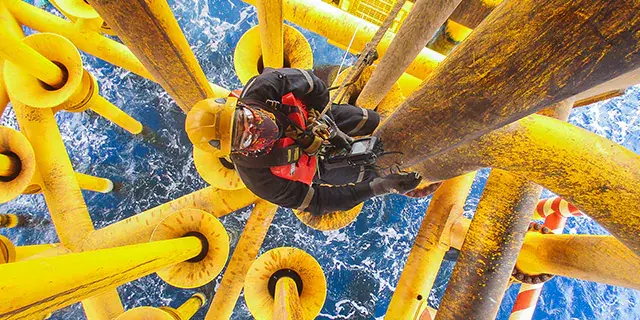
Enhance Safety and Save with Optimized Materials
Cost optimization is one of the most important goals for owners of offshore oil and gas platforms and floating vessels—second only to ensuring safe and compliant operation throughout the platform’s life span.
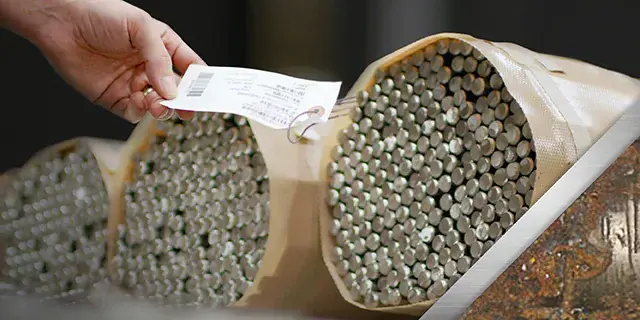
Materials Matter: Selecting the Right Material for Corrosion Resistance
An offshore platform can have nearly 50,000 feet of tubing, more than 20,000 fluid system components, no fewer than 10,000 fittings, and as many as 8,000 mechanical connections.
Need more information, support, or quotation?
Give us a call at 603.8084.1818 or email us.